Ultrasonic testing has been around for years. However, it has only been recently that advancements in technology as well as a better understanding of ultrasonic’s as a whole have allowed considerable advancements and the use of this technology within industry. Today Ultrasonic’s are employed in detecting industrial leaks and emissions.
Leak Detection. Leaks produce ultrasonic emissions therefore they can be identified and located. Leaks from piping can also be located:
- In walls, ceilings and floors
- Underground, through pavement, soil and concrete.
- Through insulation, cladding. and coatings
- Pressure or Vacuum systems
Electrical Inspections. Inspecting High Medium and low voltage equipment without opening panels or exposing components. This considerably reduces the inspection time and eliminates hazards associated with electricity. Ultrasonic’ testing is the only way to identify Corona in High Voltage systems over 1000 volts.
Mechanical Inspections. Identify bearing condition and lubrication characteristics with either comparative or historical data. Identifying single point components allows for repair without triggering a major overhaul in many cases.
Leak Detection
- Capable of detecting a 5 psi leak of “any gas” from a .005” hole from 50 feet away.
- Detect vacuum leaks, hatch leaks
- Detect leaks regardless of ambient noise or weather conditions
- Find Underground leaks
Electrical Inspections
- Identify Corona, Arcing and Tracking without opening panels or interfering with components in any way.
Mechanical Inspections
- Utilizing Historical or Comparative analysis, beginning, advanced or imminent bearing failure can be identified.
- Over or under lubrication identified
- Valve and Steam Trap Testing
- Pump Cavitation
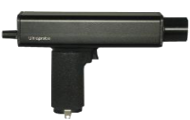